Electron beam powder bed fusion is a metal additive manufacturing technology that holds immense promise with its ability to make complex metal parts that are difficult or unachievable through conventional manufacturing approaches.
This technology has a wide range of applications, from 3D printing titanium aluminide for making jet engine turbine blades to creating personalized biomedical implants and prosthetics.
However, the dynamics of this additive manufacturing process largely remain a mystery, which has held back the development and adoption of electron beam powder bed fusion technology in industry.
“Without a better understanding of the process dynamics, we don’t know what causes defects in manufactured parts,” says Lianyi Chen, Charles Ringrose Assistant Professor in mechanical engineering at UW-Madison. “So it’s critical to learn more about the process in order to develop improved electron beam additive manufacturing technologies that can mitigate or eliminate defects.”
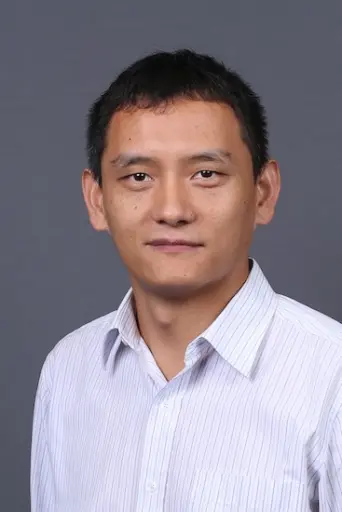
Chen is leading a unique team that aims to significantly improve measurement and understanding of the electron beam powder bed fusion process. The research will enhance U.S. manufacturers’ ability to use this technology to make high-quality, innovative and complex products at high volume. A two-year, $1 million grant from the National Institute of Standards and Technology (NIST) is supporting the project.
The electron beam powder bed fusion process involves using an electron beam to melt and fuse powdered metal together under a vacuum to build 3D parts layer by layer. After the electron beam melts a layer of the metal powder to the product, a new thin layer of powdered metal is rolled onto the working area of the powder bed to build the next layer of the product.
The researchers will develop a testbed for in-situ monitoring of the process dynamics beneath the surface of the powder bed and use high-speed x-ray imaging/diffraction to quantify those dynamics.
“The testbed and protocols that we’re developing for this project will allow us to take in-situ measurements of process dynamics in the electron beam powder bed fusion process, generating knowledge that will significantly advance this additive manufacturing technology,” Chen says.
As the electron beam interacts with the powdered material, high temperatures occur and hot vapor forms in the area above the interaction zone. Chen says it’s also critical to understand the properties of the vapor, as the vaporization will affect the liquid pool, influence the absorption and change the composition of the alloy. However, the vaporization process occurs very quickly and is currently highly challenging to study.
To address this challenge, Mechanical Engineering Professor Scott Sanders is harnessing various laser and optical techniques to measure the properties of the vapor, including temperature and the composition of the gas, for the first time. Sanders is a longtime faculty member in the world-renowned UW-Madison Engine Research Center, and he will draw on his engine research expertise for this project.
“At the Engine Research Center, we have been applying optics to study hot gases in the combustion process for quite a long time. So we’re essentially leveraging that expertise for a different application—to study this additive manufacturing process,” Sanders says.
In addition, Kevin Eliceiri, an associate professor of biomedical engineering and medical physics, and Brandon Walker, a postdoctoral research associate in Eliceiri’s group in the campus-based Morgridge Institute for Research, are collaborating on the project. Walker has been developing a novel multi-source electron beam scanning system for use in metal additive manufacturing techniques for biomedical applications, and he and Eliceiri will leverage their expertise to advise the team on various applications for the technology.