If Hantang Qin and his collaborators succeed in putting their 3D-printing technology on the International Space Station, they don’t want it to merely operate in zero gravity. They want it to function autonomously, lessening the workload of space crews.
With that in mind, the University of Wisconsin-Madison engineer and his students continue to forge ahead with advances on an array of elements for such a system, which could be used to print replacement sensors and other components.
“For in-space manufacturing, there will be no human to get involved with the process,” says Qin, an assistant professor of industrial and systems engineering. “So this kind of autonomous concept is quite important.”
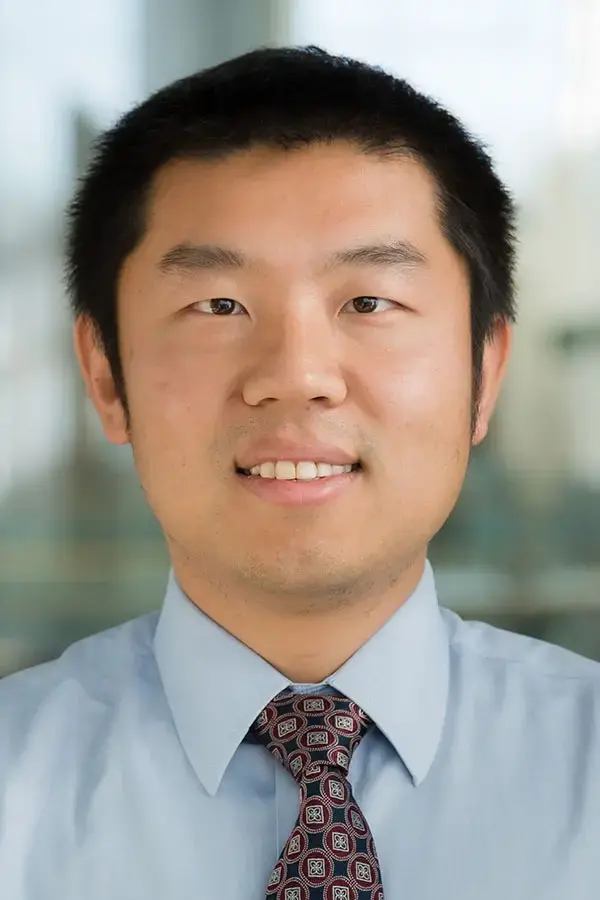
Qin’s lab has published three recent papers outlining research to further develop its electrohydrodynamic printing technology: a way to enhance printing quality monitoring, a key piece of enabling future autonomous systems; a new type of ink that allows for printing on flexible materials; and a data science method for using on-ground experiments to predict performance in zero-gravity conditions.
Two of the papers appear in the Journal of Manufacturing Science and Engineering, while the other appears in ACS Applied Materials & Interfaces and is part of an ongoing collaboration with materials science researchers at Iowa State University.
PhD student Liangkui Jiang, the first author on two of those papers and second author on the other, is the longest-serving member of Qin’s lab, having worked on two generations of the 3D printing system. He followed Qin to UW-Madison from Iowa State in 2022.
Jiang says the quality-monitoring system, which combines machine learning and machine vision to analyze low-fidelity camera data and predict final printing resolution, is the first step toward an autonomous system.
“Most cameras and optical lens are not able to capture submicron features. We don’t need such information in our prediction,” he says. “The next step is we need feedback controls to make the whole system autonomous.”
The group’s silver ink, developed by the lab of Shan Jiang, an associate professor of materials science and engineering at Iowa State, was produced using a polymer called 2-hydroxyethyl cellulose, rather than the polyvinylpyrrolidone that’s traditionally used. The group’s new ink has a lower sintering temperature—the point at which heat and pressure form a solid without first melting to liquid—which makes it a good fit for printing on flexible plastics (polymers). It also holds up better than the standard ink.
“We can store it for a long time, it has good stability, and after that we can still have good printing,” says Jiang.
The Qin lab’s method for predicting in-space printing performance from on-ground experimental data—work led by PhD student Rayne Wolf—relies upon a machine learning technique called transfer learning. Given the cost of transporting equipment and conducting parabolic test flights to simulate in-space conditions, the method could accelerate progress toward in-space manufacturing by allowing researchers to more rapidly perform experiments in standard lab environments.
“We don’t have unlimited resources to do the tests in zero gravity,” says Qin.
Qin’s team, which successfully printed RAM device units in zero gravity for the first time in March 2024, participated in another round of parabolic test flights in August 2024 and has additional trips on the horizon.
Meanwhile, Jiang will complete his PhD in fall 2025 and hopes to land a faculty position. He’s keen to continue his work in academia.
“I feel like I have a lot of crazy ideas and energy and enthusiasm,” he says.
Top photo caption: PhD student Liangkui Jiang has worked on the zero-gravity 3D printing project since its inception. Photo: Tom Ziemer.