A team of University of Wisconsin-Madison materials scientists have shown that a material they discovered via advanced computational simulation can, in real life, improve the performance of electrodes in solid oxide fuel cells.
While the advance could help improve the affordability and operation of the fuel cells, a promising form of alternative energy, it also validates the power of big data and computer modeling to accelerate fundamental materials research and discovery.
Led by Ryan Jacobs, a scientist in materials science and engineering at UW-Madison, and Dane Morgan, a professor of materials science and engineering, the team published its results in the May 2022 issue of the journal Advanced Energy Materials.
Solid oxide fuel cells convert fossil fuels or hydrogen into electricity. But because the technology extracts energy from the fuels electrochemically, it is much more efficient and less polluting than combustion engines. They are a promising technology to make more efficient use of today’s fuels and future green fuels, which are produced from renewable sources, like biofuels or hydrogen from solar-powered water splitting.
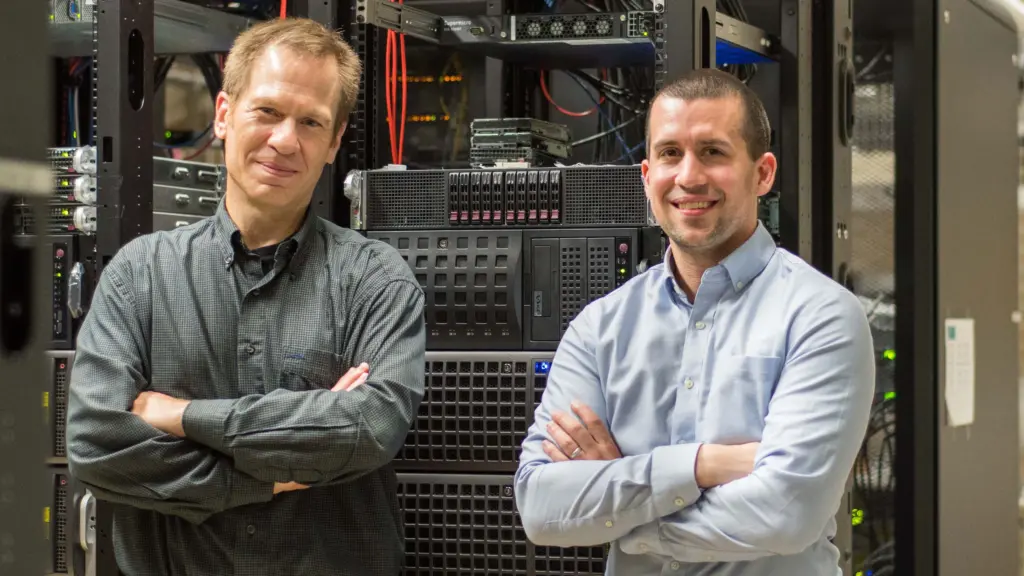
Fuel cells operate similarly to batteries in that they use two electrodes, an anode and cathode, separated by an electrolyte. In the case of solid oxide fuel cells, the electrolyte separating the electrodes is not a liquid, but a solid ceramic. On one side, a cathode catalytically splits oxygen into ions. These oxygen ions then travel through the electrolyte to the anode, where they react with the hydrocarbon fuel. This fuel-side reaction releases electrons, creating a flow of electricity.
While solid oxide fuel cells are currently available commercially, there is still a lot of room for improvement to foster more widespread adoption. The fuel cells operate at temperatures exceeding 1,500 degrees Fahrenheit, meaning the materials used in them need to be extremely durable for long operational periods. Lowering the temperature of solid oxide fuel cells is a promising approach to more economically feasible fuel cell production and operation. However, reducing the temperature also reduces the catalytic performance of the fuel cell cathode, hampering the cell’s performance.
Catalyzing the oxygen reduction reaction at the cathode also needs to be more efficient to make the devices more economically feasible—and one way to improve it is to use more reactive materials capable at operating at reduced temperatures without sacrificing long-term material durability.
In the lab, synthesizing and testing the sheer quantity of material options available could take decades. That’s why Jacobs and Morgan began using advanced quantum mechanics-based computational methods to quickly assess perovskites, materials with a particular crystalline structure which are the main materials used as solid oxide fuel cell catalysts.
“We searched through thousands of materials computationally, looking for catalysts for fuel cells that were high performing and stable,” says Jacobs. “We were looking for materials expected to be highly active, stable, electrically conductive, and made of earth-abundant materials. We found a number of materials that were potentially interesting, and chose a couple based on how easily we felt we would be able to make them in the lab. We eventually landed on the material that became the focus of this work.”
“It is important to realize that the calculations do not tell us everything about the material, and there is still a lot of work to discover a high-performing commercially viable material even with the computer guidance,” says Morgan. “The calculations provide a much more targeted list to study experimentally than just using intuition. This list reduces the number of possible systems from thousands to just tens, provides suggestions that might be new compared to those derived from our previous experience, and greatly increases the chance that an experiment will find a system that can meet performance targets.”
The team identified a perovskite comprised of barium, iron, cobalt, zirconium and oxygen (BFCZ75) as the ideal candidate for synthesis and experimental testing. The material was somewhat surprising for its 75-percent content of zirconium. “In a perovskite, zirconium is a pretty inert element and doesn’t participate in the catalytic process,” says Jacobs. “For this reason, most researchers use more like 10 or 20 percent zirconium. Surprisingly, we found that even at the level of 75 percent zirconium, the material is still highly active.”
Jacobs worked with researchers at the Department of Energy’s National Energy Technology Laboratory (NETL) in West Virginia, who synthesized BFCZ75 and tested it as a component of fuel cell electrodes. The team mixed the perovskite with those of the commercial cathode materials lanthanum strontium manganite and lanthanum strontium cobalt ferrite at the granular level. When they put cathodes made from those materials into solid oxide fuel cells, they found that the mixed materials increased the activity of the commercial cathodes by a factor of five to 10. “What’s also cool is that the BFCZ75 improved the stability of the composite electrode,” says Jacobs.
“The successful demonstration of BFCZ75 in practical cathode application challenges the conventional chemical intuition in solid oxide fuel cell design. It opens up the opportunity to utilize a new class of materials possessing superior combinations of oxygen exchange activity and durability that are not all accessible from typical highly electrically conductive perovskites,” says Jian Liu, who led the experimental effort at the NETL.
The other virtue of BFCZ75 is that its successful integration with commercial cathode materials means it could be a plug and play solution for industry instead of redesigning the entire cathode.
Jacobs says that not long ago, a material like BFCZ75 would have been dismissed out of hand since its high zirconium was thought to yield poor performance. Its discovery proves, however, that modern computational-based materials modeling can point to unconventional and novel design strategies that might buck conventional wisdom.
“The material’s behavior agreed with our computational predictions,” says Jacobs. “It’s exciting to see predictions of material performance from computer simulation persist to real-life experiments done in the lab, and to see them point to new possible material design strategies for improved fuel cell cathodes.”
Dane Morgan is the Harvey D. Spangler Professor of Engineering. Other authors include Jian Liu, Beom Tak Na, Bo Guan, Tao Yang, Shiwoo Lee, Greg Hackett, Tom Kalapos and Harry Abernathy of the Department of Energy National Energy Technology Lab. The authors acknowledge funding by the United States Department of Energy, National Energy Technology Laboratory, in part, through a site support contract.
Top image caption: Jian Liu of the Department of Energy’s National Energy Technology Laboratory in West Virginia synthesized and tested the new cathode material identified at UW-Madison.