Using hydrocarbon seeds, materials engineers at the University of Wisconsin-Madison have developed a new method for making graphene nanoribbons. In the future, the technique may allow the industrial-scale fabrication of the ribbons, enabling them to be used as next-generation transistors on computer chips and other “post-silicon” devices.
Led by Michael Arnold, a professor of materials science and engineering at UW-Madison, and PhD graduate Austin Way, the research appears in the June 2022 issue of the journal Nature Communications.
For the last half century, the world has relied on silicon transistors to provide ever-increasing amounts of computing power. But sometime soon, manufacturers will reach a physical limit where it’s no longer possible to cram more silicon transistors onto a chip. That’s why researchers are searching for the next great semiconductors—materials that can continue to improve and evolve microprocessors and other nanoelectric devices. Graphene nanoribbons, a one-atom-thick material just 3 nanometers wide, are one of the most promising candidates because of their potential to conduct five to 10 times more current than silicon and use just one-fifth to one-tenth of the power.
But taking graphene nanoribbon transistors from the lab to a smartphone is challenging. While methods for growing large-area, 2D sheets of graphene are maturing, researchers still must figure out better ways to fabricate ultranarrow graphene nanoribbons. Having narrow widths is critical because it is the narrowness of the nanoribbons that transforms them into semiconductors, whereas 2D sheets of graphene act more like metals.
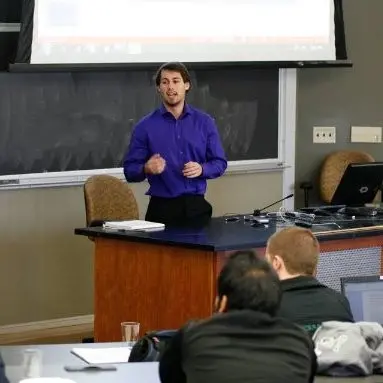
“The question is how do you take this 2D material and scale it down to a regime that is useful for semiconductors?” says Way, now an engineer at ASM in Scottsdale, Arizona. “And then how do you scale it to a point where you can actually control it so it’s useful in industry?”
In previous experiments, the team exposed a special type of substrate comprised of germanium to methane vapor, which caused graphene ribbons to grow. However, at that point, ribbon growth was sporadic and unorganized, and the strips tended grow with non-uniform widths. That impacts their electrical properties.
Way looked for methods to grow the ribbons in a more controlled manner. Initially, he decided to try lithography, which is currently used to create silicon transistors, etching 10-nanometer graphene dots on a germanium substrate and then using vapor methane deposition to induce the ribbons to grow. While the process showed promise, 10 nanometers was still much too wide for a functional nanoribbon (3 nanometers wide is ideal for a bandgap that allows it to work as a transistor).
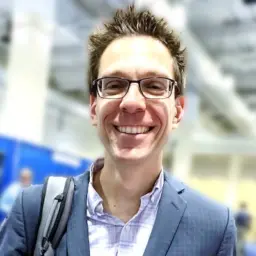
“We had to come up with an alternate idea,” says Arnold. “We thought it would be really cool if we could use a baby, graphene-like molecule as a seed instead.”
They decided to try PTCDA, a polycyclic aromatic hydrocarbon, which is part of a class of molecules that are very flat and resemble tiny pieces of graphene. Way first exposed a germanium wafer to a vapor of PTCDA molecules, which landed on the surface, essentially scattering the PTCDA seeds. He then flowed methane over the substrate, and that reacted with the seeds. As the graphene formed, it followed the crystalline structure of the germanium, resulting in long thin ribbons, all forming on roughly the same time scale. By using a technique employing miscut, or stair-step surfaces on the germanium, the team also better controlled the orientation of the ribbons.
Afterwards, the researchers examined the ribbons using a scanning tunneling microscope at Argonne National Laboratory. They found that they had relatively smooth “armchair” edges, which are needed to function as transistors.
In future work, Arnold says he would like to refine the process and chemically “passivate” the edges of the ribbons, which are prone to oxidation. He would also like to better understand the process by using microscopy to watch the ribbons form.
“To really get to the point where I would say it’s truly scalable as a technique, we need to get that fundamental understanding first,” says Way, who says these techniques could also be used with other 2D materials. “We want to learn and understand how the seeds are distributed on the surface, and how density is impacted by that. That level of control and understanding is the next step in terms of synthesis.”
While there are still many hurdles to overcome before graphene nanoribbons end up on a commercial computer chip, Arnold thinks there’s a path forward for the technology. “You could take a silicon wafer with germanium on it, then grow the graphene nanoribbons on top of that,” he says. “There is the promise at least of being able to integrate our technology directly into silicon wafer technology.”
Other UW-Madison authors include post-doctoral researcher Robert Jacobberger; graduate students Vivek Saraswat, Xiaoqi Zheng, Anjali Suresh, Jonathan Dwyer; and Padma Gopalan, a professor of materials science and engineering.
Nathan Guisinger from Argonne National Laboratory also contributed to the paper.
The authors acknowledge support from the U.S. Department of Energy, Office of Science, Basic Energy Sciences, under award no. DE-SC0016007; The Center for Nanoscale Materials, a U.S. Department of Energy Office of Science User Facility, supported by the U.S. Department of Energy, Office of Science, under Contract No. DE-AC02-06CH11357; U.S. Defense Advanced Research Projects Agency Grant No. D18AP00043; The University Joint Development Project program of Taiwan Semiconductor Manufacturing Company; and the use of facilities and instrumentation supported by NSF through the University of Wisconsin Materials Research Science and Engineering Center (DMR-1121288, 0079983, and 0520057) and through the University of Wisconsin Nanoscale Science and Engineering Center (DMR-0832760 and 0425880).